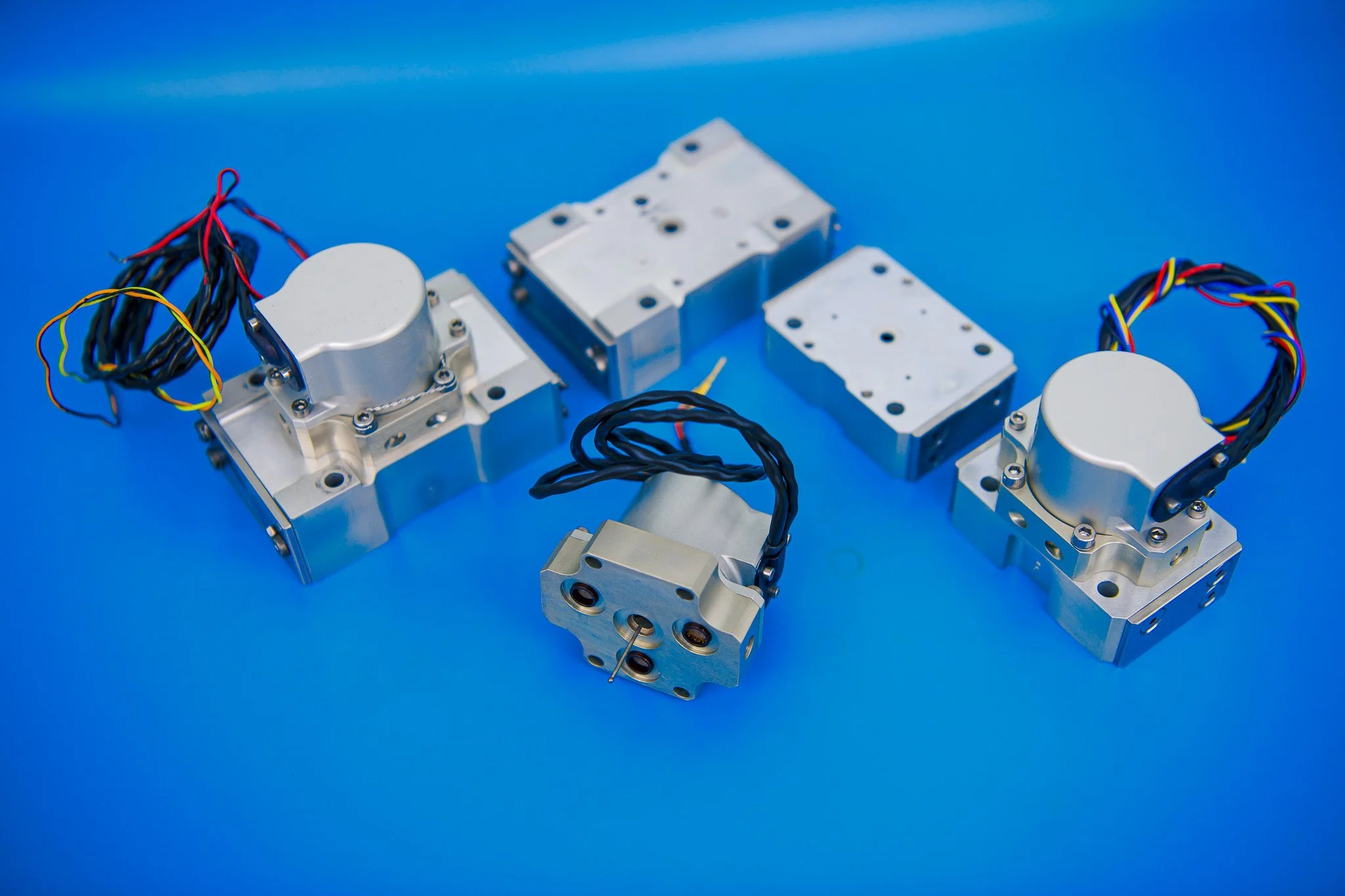
Our Process
A Modular
Engineering Approach
Servotronics Specializes in Application-Specific Hydraulic and Pneumatic Servo Valves.
Unlike traditional catalog suppliers, Servotronics takes a collaborative approach to servo valve precision. We partner with customers to optimize cost-effective solutions that meet the requirements of your application and use our fast-turnaround modeling tools to configure our flexible building blocks and deliver designs that meet your requirements.
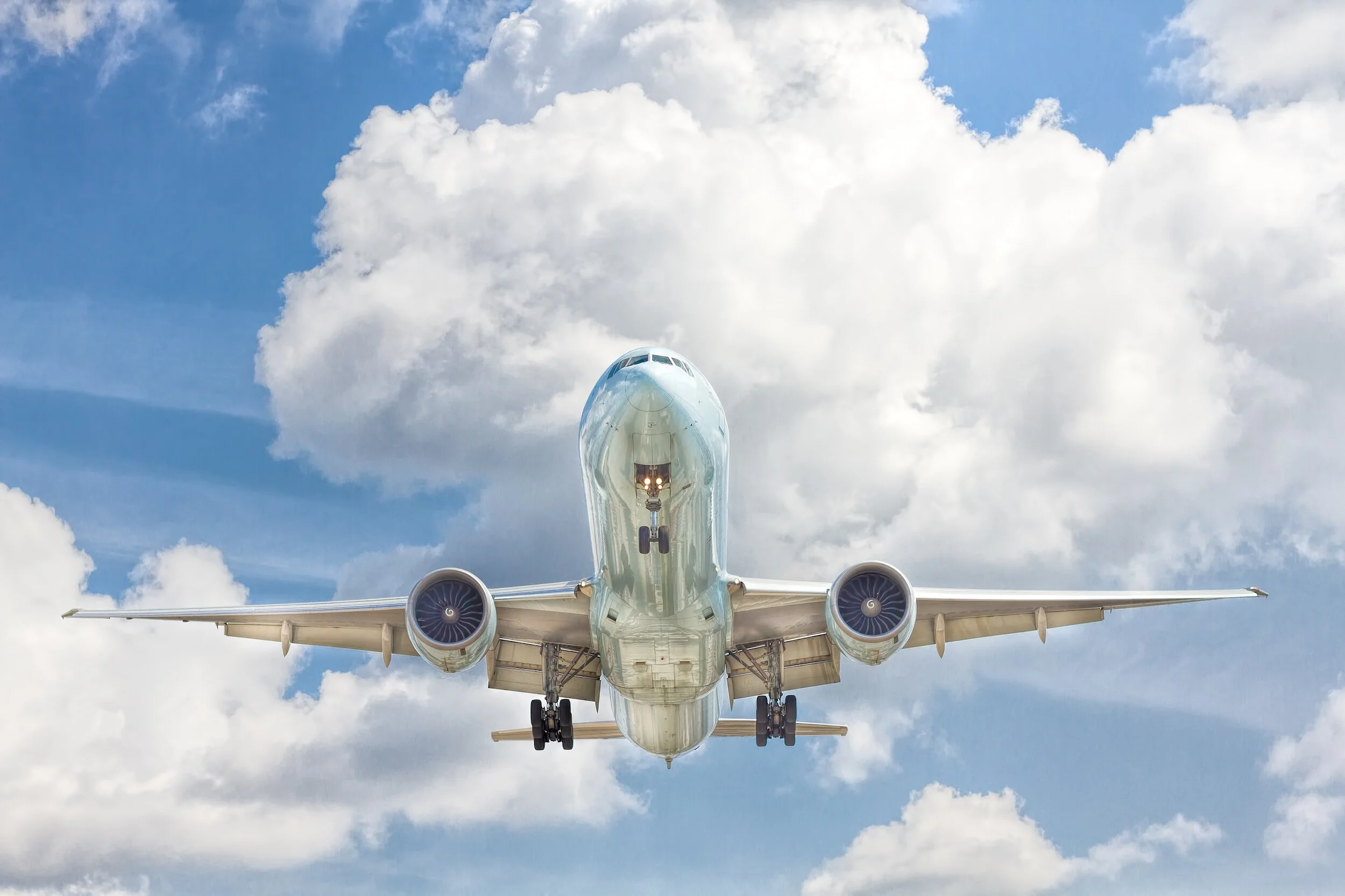
Our proven process.
1
Common modular building blocks are used to improve lead time, reliability, and cost
2
Analytical design tools predict performance and capability
3
Onsite design validation of capability
4
Dedicated engineering and program management
Industry Leading Building
Blocks
Servotronics leverages our established coils and torque motor components to create a valve design that meets all your requirements.
In addition, we have established standardized subcomponents for the fluid metering section. This means regardless of whether your application necessitates a nozzle flapper, clevis, or bushing spool architecture, our engineers will utilize our proven standardized subcomponents to fulfill your requirements, providing competitive lead times and pricing.
Application Requirements
Temperature: -65°-450°F (-54°-232°C)
High Vibration: up to 100 G (20 Hz-4000 Hz)
Operating: 5-3500 psig (241 bar)
Performance Capabilities
Hysteresis: <2% rated current
Threshold: <0.5% rated current
Fuel: MIL-7024, Red Oil Fuel, Pneumatic
Low Weight: <0.5 lbs (single stage)
Common Building Blocks
Core Torque Motor Options
Servotronics has several aerospace-qualified torque motor designs to fit a variety of applications. Our engineers will select the best torque motor to suit your application. Additionally, we have standardized qualified subcomponents for the fluid metering section. So, whether your application requires a nozzle flapper, clevis, or Bushing spool architecture, our engineers will use our tried and true standardized subcomponents to accommodate your request offering competitive lead times and pricing.
Flexure Tube Design
Click image to enlarge
A Stainless or titanium tube forms both a hydraulic seal and provides a spring function for the armature and flapper.
The torque motor coil, magnets, and pole pieces transform electrical current (mA) into magnetic flux carried by the armature. The result is precision motion to change the flapper position between nozzles, with zero mechanical friction. Heat treated precision adjusted pole pieces allow for minimum hysteresis and accurate positioning with respect to current. Servotronics Flexure tube torque motors do not require damping fluid and can be adapted to any nozzle flapper configuration.
Spring Armature Flapper Assembly (SAFA) Design
Click image to enlarge
Our flagship torque motor does not require damping fluid and can be adapted to all hydraulic servo valve architectures, including jet pipe, clevis, and nozzle flapper.
A small O-ring forms the hydraulic seal, while a rigid torsion bar spring provides the suspension and spring function. The torque motor coil, magnets, and pole pieces transform electrical current (mA) into magnetic flux carried by the armature. The result is precision motion to change the flapper position, with near zero mechanical friction, increased torque, and longer linear stroke, with phenomenal tolerance to high vibration.
Adaptable features & options.
Footprint Size
Envelope Size
Mounting Patterns
Electrical Connectors
Linear Variable Differential Transducers (LVDT)
Pressure Transducers
Heaters
Wire Exit Locations

Are you ready to get started?
Submit a Request for Information or Request for Quote
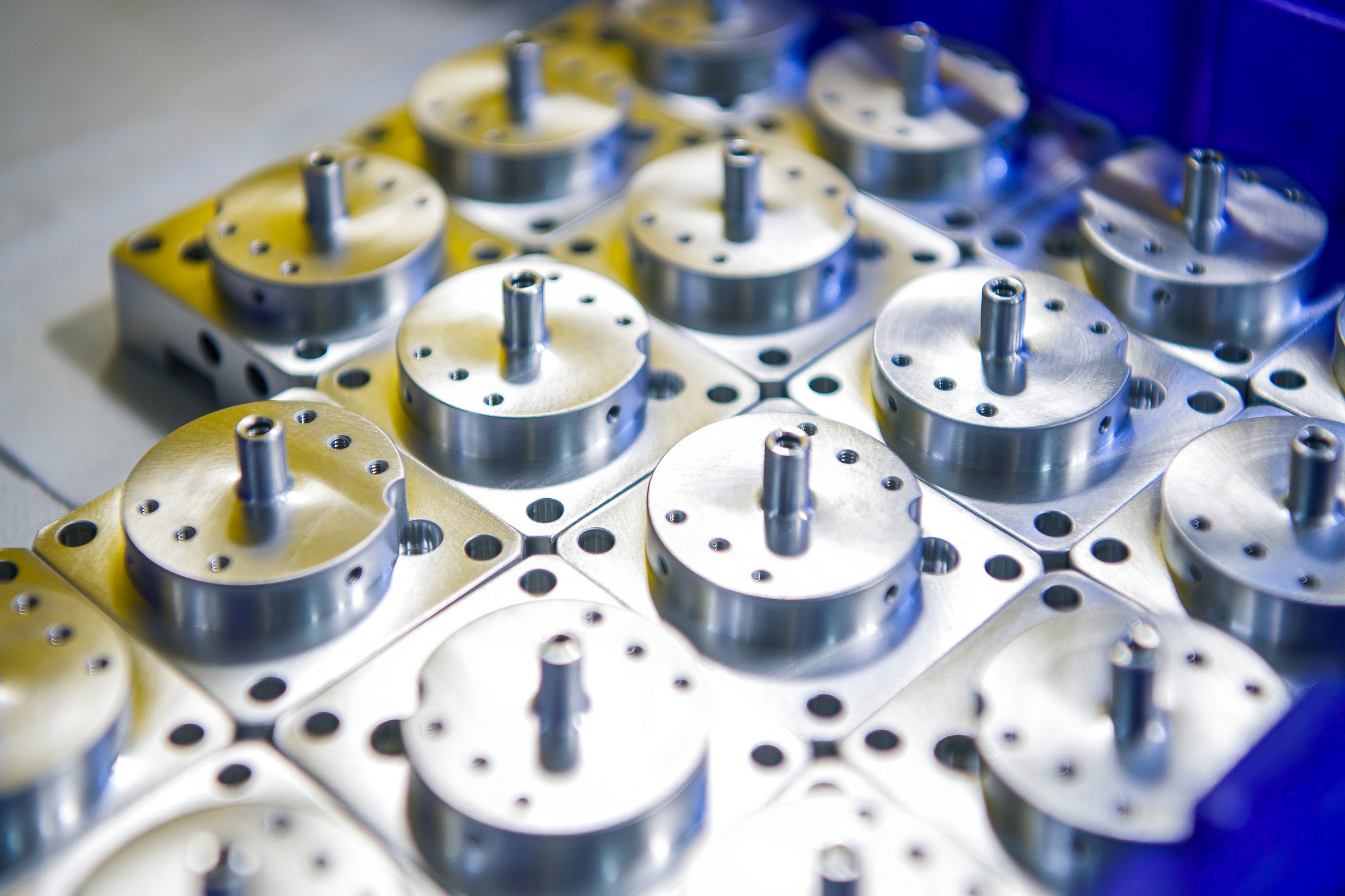